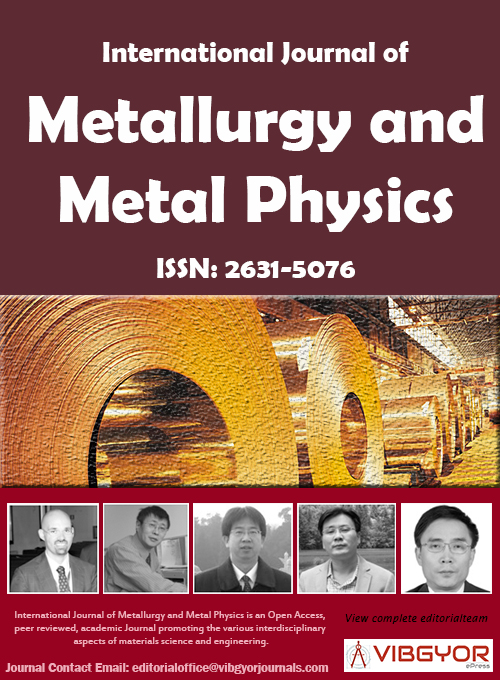
International Journal of Metallurgy and Metal Physics
(ISSN: 2631-5076)
Volume 3, Issue 2
Research Article
DOI: 10.35840/2631-5076/9224
Effect of One Step In-Mould Inoculation Method on the Characterization of Thin Wall Ductile Iron
Rajat Upadhyaya1*, Kamlesh Kumar Singh1, Rajeev Kumar2 and Himanshu Pathak3
Table of Content
Figures

Figure 2: Microstructure of 2 mm section thickness...
Microstructure of 2 mm section thickness inoculated by Ce-Ca-Al-S-O-FeSi. a) 0.2 wt%; b) 0.4 wt%; c) 0.6 wt% one step in-mould inoculation.

Figure 3: Microstructure of 2 mm section thickness...
Microstructure of 2 mm section thickness inoculated by Zr-Mn-Ca-Al-Ba-FeSi. a) 0.2 wt%; b) 0.4 wt%; c) 0.6 wt% one step in- mould inoculation.

Figure 4: The Microstructure of 2 mm section thickness inoculated...
Microstructure of 2 mm section thickness inoculated by Sr-Al-Ca-FeSi. a) 0.2 wt%; b) 0.4 wt%; c) 0.6 wt% in-mould inoculation.

Figure 5: 2 mm section thickness of SEM with EDS micrograph inoculated...
2 mm section thickness of SEM with EDS micrograph inoculated by a) Ce-Ca-Al-S-O-FeSi; b) Zr-Mn-Ca-Al-Ba-FeSi; c) Sr-Al-Ca-FeSi at 0.4 wt% one step in-mould inoculation.

Figure 6: 2 mm section thickness of Tensile SEM fractograph...
2 mm section thickness of Tensile SEM fractograph inoculated by a) Ce-Ca-Al-S-O-FeSi; b) Zr-Mn- Ca-Al-Ba-FeSi; c) Sr-Al-Ca-FeSi at 0.4 wt% one step inmould inoculation.

Figure 7: SEM fractograph of 2 mm impact sample inoculated...
SEM fractograph of 2 mm impact sample inoculated by a) Ce-Ca-Al-S-O-FeSi; b) Zr-Mn-Ca-Al-Ba- FeSi; c) Sr- Al-Ca-FeSi at 0.4 wt% one step in-mould inoculation.
Tables
Table 1: Final charge metal composition (in weight percentage).
Table 2: Nodulization treatment FeSi (7-8%) Mg alloy composition (in percentage).
Table 3: Composition of Inoculants (in percentage).
Table 4: 2 mm section thickness tensile data. a) Ce-Ca-Al-S-O-FeSi; b) Zr-Mn-Ca-Al-Ba-FeSi; c) Sr-Al-Ca-FeSi at 0.4 wt % one step in-mould inoculation.
Table 5: 2 mm section thickness impact data inoculated by a) Ce-Ca-Al-S-O-FeSi; b) Zr-Mn-Ca-Al-Ba-FeSi; c) Sr-Al-Ca-FeSi at 0.4 wt% one step in-mould inoculation.
References
- Karsay SI (1965) Production of thin As-Cast ductile iron. Modern Castings 124-133.
- Mampaey F, Xu ZA (1997) Mold filling and solidification of a thin-wall ductile iron casting. AFS Trans 105: 95-103.
- Yeunga CF, Zhaoa H, Leea WB (1998) The morphology of solidification of thin section ductile iron castings. Material Characterization 40: 201-208.
- Ruxanda RE, Stefanescu DM, Piwonka TS (2002) Microstructure characterization of ductile thin wall iron castings. AFS Trans 110: 1131-1147.
- David P, Mossone J, Boeri R, Sikora J (2009) Gating system design to cast thin wall ductile iron plates. Foundry Trade Journal 182: 119-126.
- Banerjee DK, Stefanescu DM (1991) Structure transitions and solidification kinetics of S.G cast iron during directional solidification experiment. AFS Trans 99: 747-759.
- Woolley JM, Stefanescu DM (2005) Microshrinkage propensity in thin wall ductileiron casting. AFS Trans 637-643.
- Dix LP, Ruxanda R, Torrance J, Fukumato M, Stefanescu DM (2003) Static mechanical properties of ferritic and pearlitic lightweight ductile iron castings. AFS Trans 111: 1149-1164.
- Chisamera M, Riposan I, Stan S, Toboc P, Skaland T, et al. (2013) Shrinkage evaluation in ductile iron as influenced by mould media and inoculant type. International Journal of Cast Metal Research 24: 28-36.
- Skaland T (2001) A new approach to ductile iron inoculation. Transaction American Foundry Society 28: 1-12.
- Choi JO, Kim JY, Choi CO, Kimb JK, Rohatgi PK (2004) Effect of rare earth element on microstructure formation and mechanical properties of thin wall ductile iron castings. Mater Sci Eng A 383: 323-333.
- Riposan I, Chisamera M, Uta V, Stan S, Naro R, et al. (2014) The Importance of rare earth contribution from nodulizing alloys and their subsequent effect on the inoculation of ductile iron. Int J Met Casting 8: 65-80.
- Ochulor EF, Adeosun SO, Amuda MOH, Balogun SA (2015) Strength characteristics of inoculated and nodularised thin wall ductile iron castings. Journal of Minerals and Materials Characterization and Engineering 3: 94-105.
- Upadhyaya R, Singh KK, Kumar R (2017) Microstructure and mechanical properties of thin wall ductile iron. Journal of Automobile Engineering and Applications 4: 35-39.
Author Details
Rajat Upadhyaya1*, Kamlesh Kumar Singh1, Rajeev Kumar2 and Himanshu Pathak3
1Department of Foundry Technology, National Institute of Foundry and Forge Technology, India
2Department of Mechanical Engineering, Birla Institute of Technology, India
3School of Engineering, Indian Institute of Technology, India
Corresponding author
Rajat Upadhyaya, Department of Foundry Technology, National Institute of Foundry and Forge Technology, Ranchi, Jharkhand, India.
Accepted: November 14, 2018 | Published Online: November 16, 2018
Citation: Upadhyaya R, Singh KK, Kumar R, Pathak H (2018) Effect of One Step In-Mould Inoculation Method on the Characterization of Thin Wall Ductile Iron. Int J Metall Met Phys 3:024.
Copyright: © 2018 Upadhyaya R, et al. This is an open-access article distributed under the terms of the Creative Commons Attribution License, which permits unrestricted use, distribution, and reproduction in any medium, provided the original author and source are credited.
Abstract
This research work concerns an assessment of the effect of one step in-mould inoculation method on thin section castings 2 mm analyzed. In this study inoculants representing Ce, Zr and Sr bearing Fe-Si alloys were used. It has been observed that section thickness of 2 mm thin plate containing Ce bearing Fe-Si alloys at 0.4 wt% contain mainly pearlitic matrix having ultimate tensile strength (UTS), impact energy and percentage of elongation are 720 MPa, 75.28 J/cm2 and 4.5% respectively. It was observed that 2 mm section thickness of thin plate containing Ce bearing Fe-Si alloys have greater ultimate tensile strength compare to Zr bearing Fe-Si alloys and Sr bearing Fe-Si alloys respectively at 0.4 wt% due to reason of pearlitic and ferritic volume fraction contents present in matrix.
Keywords
Thin wall ductile iron, Simulation, One step in-mould inoculation
Introduction
Unlike gray iron whose production tends to stagnate, ductile iron enjoy growth exceeding 3% per year [1]. In the recent years basically interest on minimizing the weight of casting components and increasing the mechanical properties. This motivates automobile manufacturers to decrease the weight of automobile leads in the 1970's by reducing the thickness of steel sheets [2-4]. Inoculation which is a means controlling the structure and properties of cast irons by increasing the number of nucleation sites available for the growth of graphite nodules is an important part in the treatment enacted to obtain the desired result. Inoculation treatment is very important because it improves the homogeneity of the cast iron structure, it helps to eliminate the formation of carbides into thin parts or salient angles and promote the formation of graphite during eutectic solidification, direct the solidification towards the stable diagram, with graphite precipitation, refine the structure (higher cells count, finer grains in the microstructure) etc. Inoculation is to increase the number of nuclei in molten iron so that eutectic solidification, specifically graphite precipitation, can begin with a minimum amount of undercooling. When undercooling is minimized, there is a corresponding reduction in the tendency to form eutectic carbide or white iron. Inoculation is defined as the late addition of certain silicon alloys to molten iron to produce changes in graphite distribution, improvements in mechanical properties, and a reduction of the chilling tendency that are not explainable on the basis of composition change with respect to silicon [5]. Various studies analysed the separate and combined effects of Ce (cerium) and La (Lanthanum) on the microstructure evolution and graphite morphology and they also found that La (Lanthanum) either alone or in combination with Ce (cerium) has a detrimental effect on nodule count and significant amount of carbide is formed in La (Lanthanum) containing iron whereas Ce (cerium) results in a significant drop in the extension of carbide zone [6-9]. Skaland, et al. [10] proposed that carbon diffusion towards nuclei centre may due to formation of cerium-calcium- sulphides and oxides increases the nodule count of Ce containing inoculants. Choi, et al. [11] have reported that the rare earth (RE) elements are helpful in reducing chill and influencing the formation of ferrite. Riposan, et al. [12] have investigated that the addition of rare earth elements during in-mould inoculation provides control of casting hardness and improve graphite quality. Ochulor, et al. [13] found that two step inoculation methods provide better nodule count and nodularity with 2, 3 and 4 mm thin plate thickness respectively. Upadhyaya, et al. [14] proposed that Ce bearing Fe-Si alloy at 0.4 wt% reducing under-cooling to improve nodularility and nodule count in thin plate casting thickness.
In this paper previous studies have not been reported the methodology of one step in-mould inoculation method. The present work concerns an assessment of representing three types of potent inoculants containing Ce, Zr and Sr bearing Fe-Si alloy at an addition rate of 0.2 wt%, 0.4 wt% and 0.6 wt% of one step in-mould inoculation method. It can be seen that Ce bearing Fe-Si alloy at 0.4 wt % provides better mechanical properties, nodule count, nodularity (> 90%) and nodule size distribution as compare to Zr bearing Fe-Si alloys and Sr bearing Fe-Si alloys. The as-cast and austempered microstructure samples were characterized by metallurgical optical microscopy (LIECADM2500) and scanning electron microscopy (SEM-JEOL JSM 6390LV). Mechanical properties were investigated by tensile and impact test. The fracture surfaces of tensile were also evaluated by scanning electron microscopy (SEM-JEOL JSM 6390LV).The final results of this characterization will be discussed.
Materials and Methods
Melting of SG (Spheroidal graphitic) Iron heat was taken out in a coreless induction furnace of 1 ton capacity. The tapping temperature of liquid metal from furnace to preheated ladle at 1430 ℃ - 1460 ℃ [14]. The final charge metal composition is shown in Table 1.
Sandwich method has been done for magnesium treatment. The composition of nodulization treatment alloys summarized in Table 2.
The preheated pouring ladle has been used for tapping molten metal from an inductance furnace and rapidly poured into magnesium treated ladle. The magnesium treated melt has been directly poured into mould cavity in addition rate of 0.2 wt%, 0.4 wt% and 0.6 wt% one step in-mould inoculation. The thin plate section thickness (2-5) mm of ductile iron castings have been shown in Figure 1. Table 3 enlist the composition of inoculants.
The metallographic preparations have standard techniques. The samples were cut into desired size and in the desired direction, mounted with bakelite powder and polished using different grades of silicon carbide emery paper starting from coarse to fine size (320, 400, 600, 800, 1000, 1200 and 2000 grits). The samples were cloth polished using alumina and diamond paste (15, 6, 0.5 µm) with diamond lubricating oil. Finally, the samples were thoroughly cleaned using ethanol in an ultrasonic cleaner for about 10 min. The microstructure was examined by subsequent etching using 2% nital solution. The mounting and polishing machine of (METCO 2500) were used for samples preparation.
The etched specimens were examined under metallurgical optical microscope (LEICA DM2500). The optical microscope equipped with image analysis software, a camera and a computer was used for quantitative measurements of microstructural feature. A software application was used to acquire images from the camera and to perform image analysis. Noularity and nodule count values were analyzed using Image-Pro Plus software. Using scanning electron microscope (SEM), a more detailed examination of the ferrite and pearlite structure of the received sample was performed. The polished specimens were thoroughly cleaned using ethanol in an ultrasonic cleaner. The etched specimens were finally observed under scanning electron microscope (JEOL JSM 6390LV) using secondary electron mode. The tensile tests samples were prepared from plate of 2 mm thickness as-cast and heat treated plates on three jaw chuck lathe. The dimensions of the samples were taken as per ASTM E8-04 standard. The test was performed on universal testing machine (Instron 8801) using 100 KN capacity. Impact test specimens were made as per ASTM standard E327M. The test was performed on charpy impact testing machine (Waston 20) using 5 kg weight. The reported values of all the properties are the average of testing of three specimens.
Results and Discussion
The microstructure has been seen by LEICA DM2500. The microstructure of 2 mm section thickness sample inoculated by Ce-Ca-Al-S-O-FeSi containing inoculants an addition rate of 0.2 wt%, 0.4 wt% and 0.6 wt% at one step in-mould inoculation are shown in Figure 2. It has been observed that wt% of one step in-mould inoculation increases 0.2% to 0.4% pearlitic matrix has been formed while wt% was 0.6%, the matrix has been changed to pearlitic to ferritic.
The microstructures of 2 mm section thickness sample inoculated by Zr-Mn-Ca-Al-Ba-FeSi containing inoculant an addition rate of 0.2 wt%, 0.4 wt% and 0.6 wt% at one step in-mould inoculation has been shown in Figure 3. Comparing the microstructures in Figure 2 and Figure 3, it have been observed that nodularity of graphite in 2 mm section thickness sample inoculated by Ce-Ca-Al-S-O-FeSi at 0.4 wt% is higher than Zr-Mn-Ca-Al-Ba-FeSi containing inoculant and pearlitic matrix formed.
The microstructures of 2 mm section thickness samples inoculated by Sr-Al-Ca-FeSi containing inoculant an addition rate of 0.2 wt%, 0.4 wt% and 0.6 wt% at one step in-mould inoculation has been shown in Figure 4. These microstructures also follow the same trend that nodularity of graphite is highest at 0.4 wt% with respect to nodularity at 0.2 wt% and 0.6 wt% respectively and formed also pearlitic matrix.
The SEM with EDS has been seen by JEOL JSM 6390LV. The micrographs of 2 mm section thickness sample inoculated by (a) Ce-Ca-Al-S-O-FeSi, (b) Zr-Mn-Ca-Al-Ba-FeSi and (c) Sr-Al-Ca-FeSi inoculants at 0.4 wt% one step in-mould inoculation have been shown in Figure 5. The micrograph shows the nodularity of graphite and pearlitic matrix. The SEM micrograph of 2 mm sample inoculated by Zr-Mn-Ca-Al-Ba-FeSi containing inoculant at 0.4 wt% one step in-mould inoculation has been shown in Figure 5b. Comparing the micrographs in Figure 5a and Figure 5b, it have been observed that nodularity of graphite in 2 mm samples inoculated by inoculant Ce-Ca-Al-S-O-FeSi is higher than Zr-Mn-Ca-Al-Ba-FeSi containing inoculant. This is so Ce-Ca-Al-S-O-FeSi containing inoculant has higher nodularity may be due to formation of cerium-calcium-sulphides and oxides during solidification [13,14]. It may be also noted from energy dispersive spectrometer (EDS) profile and elemental analysis that the CeO2 and Ce2S3 is observed near to the nodule point and is missing away from the nodule point. Hence, it reflects that Ce is actively taking part in formation of the nucleation site for the graphite nodules. The SEM micrograph of 2 mm sample inoculated by Sr-Al-Ca-FeSi has been given in Figure 5c which shows that nodularity of graphite and the ferrite regions around graphite nodule are because of diffusion of carbon towards graphitisation centre and also from energy dispersive spectrometer (EDS) profile and elemental analysis that SrSi is observed near to the nodule point and is missing away from the nodule point.
Tensile test results
The 2 mm tensile samples have been made according to the ASTM standard E8, which were machined to 6 mm gauge diameter and 25 mm gauge length. All tensile specimens have been performed on universal testing machine Instron 8801. The Tensile and SEM fractographs of 2 mm sample inoculated by (a) Ce-Ca-Al-S-O-FeSi, b) Zr-Mn-Ca-Al-Ba-FeSi, c) Sr-Al-Ca-FeSi containing inoculants at 0.4 wt% during one step in-mould inoculation have been shown in Figure 6 and Table 4 respectively. It has been observed that Ce-Ca-Al-S-O-FeSi for one step in-mould inoculation at 0.4 wt% contain pearlitic matrix having ultimate tensile strength (UTS) and percentage of elongation are 720 ± 3 MPa and 4.5 ± 3% which are higher than Zr-Mn-Ca-Al-Ba-FeSi (UTS and % elongation 655 ± 5 MPa and 3.3 ± 5%) and Sr-Al-Ca-FeSi (UTS and % elongation 557 ± 5 MPa and 2.3 ± 5%) respectively shown in Table 4. This is so because of carbon diffusion towards graphitization centre may due to formation of cerium-calcium-sulphides and oxides, promote the volume fraction of ferrite sample inoculated by (a) Ce-Ca-Al-S-O-FeSi, b) Zr-Mn-Ca-Al-Ba-FeSi and c) Sr-Al-Ca-FeSi increases more and volume fraction of pearlite decreases less in Ce-Ca-Al-S-O-FeSi containing inoculant [13,14]. The fracture analysis of 2 mm containing inoculants at 0.4 wt% during one step in-mould inoculation shows the mixed mode of fracture i. e. ductile and brittle fracture observed and the ductile nature of fracture can be seen more in the plates inoculated with 0.4 wt% inoculants with Ce-Ca-Al-S-O-FeSi containing inoculant. The fine pearlite for Ce-Ca-Al-S-O-FeSi containing inoculant at 0.4% may cause higher ultimate tensile strength (UTS) of pearlite and at 0.6% inoculant leads coarser pearlite and thus lower hardness of pearlite.
Impact result
All impact specimens have been performed on charpy impact tester with the strain rate of 103S-1. The test sample was prepared according to the ASTM standard E327M. It can be noted from Table 5, impact strength of Ce-Ca-Al- S-O-FeSi containing inoculant at 0.4 wt% inoculated by thin wall ductile iron sample of 2 mm section thickness have higher value compared to 2 mm section thickness of sample inoculated by Zr-Mn-Ca-Al-Ba-FeSi and Sr-Al-Ca-FeSi at 0.4 wt% during one step in-mould inoculation. This is so because of volume fraction of pearlite and ferrite present in the matrix and also SEM fractographs of 2 mm sample inoculated by Ce-Ca-Al-S-O-FeSi containing inoculant contain cerium oxide (CeO2) and cerium sulphides (CeS) present in the matrix near nodule has increases the more nuclei during solidification irrespective of Zr-Mn-Ca-Al-Ba-FeSi and Sr-Al-Ca-FeSi containing inoculants at 0.4 wt% shown in Figure 7. It may be also noted that 2 mm sample inoculated by Ce-Ca-Al-S-O-FeSi containing inoculant at 0.4 wt% shows maximum value of impact energy in compression to samples inoculated with 0.2 wt% and 0.6 wt%. The increase in impact energy for Ce-Ca-Al-S-O-FeSi containing inoculant at 0.4 wt% resulted increase in cross sectional area of fracture surface and having more volume fraction of pearlite phase and nodularity which leads to higher value of impact energy irrespective of Zr-Mn-Ca-Al-Ba-FeSi and Sr-Al-Ca-FeSi containing inoculants at 0.4 wt%. The fracture analysis of 2 mm containing inoculants at 0.4 wt% during one step in-mould inoculation shows the mixed mode of fracture i. e. ductile and brittle fracture observed and the ductile nature of fracture can be seen more in the plates inoculated with 0.4 wt% inoculants with Ce-Ca-Al-S-O-FeSi containing inoculant irrespective of Zr-Mn-Ca-Al-Ba-FeSi and Sr-Al-Ca-FeSi containing inoculants.
Conclusions
The following concluding observations may be drawn from this study:
The present study very clearly indicate that one step in-mould inoculation methodology very potent to incresase the mechanical properties of 2 mm section thickness of thin casting, especially with Ce-Ca-Al-S-O-FeSi containing inoculant. It has been observed that Ce-Ca-Al-S-O-FeSi containing inoculant at 0.4 wt% during one step in-mould inoculation contain pearlitic matrix having ultimate tensile strength (UTS), impact energy (J/cm2) and percentage of elongation are 720 ± 3 MPa 75.28 (J/cm2) and 4.5 ± 3% which are higher than Zr-Mn-Ca-Al-Ba-FeSi and Sr-Al-Ca-FeSi containing inoculants respectively. One step in-mould inoculation increases inoculant efficiency and reduces fading effect (25% of graphite nucleation loss) there by increases the nucleation sites for graphite. By increasing the wt% of one step in-mould inoculants from 0.4% to 0.6%, the matrix changes from pearlitic to ferritic. The fracture analysis of 2 mm containing inoculants at 0.4 wt% during one step in-mould inoculation shows the mixed mode of fracture i. e. ductile and brittle fracture observed and the ductile nature of fracture can be seen more in the plates inoculated with 0.4 wt% inoculant with Ce-Ca-Al-S-O-FeSi containing inoculant. The fine pearlite for Ce-Ca-Al-S-O-FeSi containing inoculant at 0.4 wt% may cause higher ultimate tensile strength (UTS) and yield strength (YS) of pearlite.
Acknowledgement
The authors are thankful to the Managing Director Mr. Dilip Kumar Gopalka of Hindustan Malleables & Forging Ltd, Dhanbad for providing the facilities of experiment and valuable comments.